寶鋼湛江鋼鐵煉鐵廠環(huán)保新工藝技術應用
2015-11-05 09:34:32
隨著一系列環(huán)保新規(guī)劃、國家標準的出臺和廣東地區(qū)對環(huán)保新的要求,湛江鋼鐵大氣污染物排放于2014年起執(zhí)行新的特別排放標準。針對環(huán)保要求的變化,湛江鋼鐵不斷優(yōu)化環(huán)保設施設計,在鐵前工序采用了多種環(huán)保新工藝技術,以滿足國家排放標準(見圖1)。
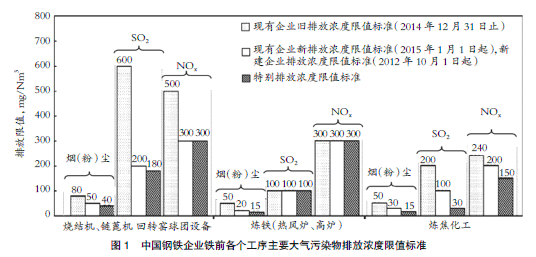
1 原料場防塵新工藝技術
原料場主要承擔了各個工序所需散狀原燃料的裝卸、貯存、加工和輸送任務,粉塵是其主要的污染物。
針對裝卸和貯存可能產(chǎn)生的粉塵污染,湛江鋼鐵的混勻料場、1個原料貯存料場和3個煤貯存料場均采取了封閉措施;1個貯存鐵礦粉的條形露天堆場,增設了20m高的防風網(wǎng),利用空氣動力學原理,使風速在防風網(wǎng)內(nèi)衰減,減小起塵率,有效阻擋粉塵遷移。原燃料的破碎加工配套了高效的布袋除塵設備。原燃料輸送采用封閉式皮帶機通廊輸送(約2.6km)和轉(zhuǎn)運站微霧抑塵裝置來控制粉塵污染。微霧抑塵原理是利用直徑為1-10μm的水霧對懸浮在空氣中的粉塵尤其是PM2.5等可入肺粉塵進行有效地吸附團聚,并在重力作用下沉降。
此新工藝減少了粉塵的收集和輸送,直接在源頭抑制粉塵的擴散。通過以上工藝的應用,原料場的粉塵排放值可達到≤15mg/Nm3。
2 煉焦煙氣凈化技術
湛江鋼鐵配置了4×65孔7m的頂裝焦爐,單座焦爐煙道廢氣(180℃)量約為0.26×106Nm3/h,其中:煙(粉)塵濃度約為20mg/Nm3;采用混合煤氣作為燃料燃燒后的SO2含量約為80mg/Nm3;采用廢氣循環(huán)和分段加熱的燃燒控制技術后NOx可降至約500mg/Nm3。然而,煙氣中主要的廢氣污染物仍無法滿足國家特排標準的要求,必須對焦爐煙氣進行脫硫脫硝凈化處理。目前,國內(nèi)外針對焦爐煙氣的脫硫脫硝技術尚處于研發(fā)階段,還未有工程應用實例。熱電廠煙氣的脫硫脫硝技術應用較為成熟,主要為“NH3-SCR煙氣脫硝+石灰石濕法脫硫”工藝,若煉焦采用相同工藝,焦爐煙氣溫度相對較低,采用中溫脫硝(300-400℃)的釩系催化劑的脫硝效率會很低,需大幅加熱煙氣;煙氣中的SO2在200-250℃極易生成具有腐蝕性的硫酸氫銨,致使催化劑中毒;采用濕法脫硫后的煙氣溫度會低于130℃,不能直接從煙囪上升排放。根據(jù)這些不同之處,湛江鋼鐵煉焦工序采用了“旋轉(zhuǎn)噴霧半干法脫硫+低溫選擇性催化還原法(NH3-SCR)脫硝除塵”工藝,成為世界上首個對鋼鐵企業(yè)焦爐煙道廢氣脫硫脫硝的工程應用實例。
煉焦煙氣脫硫脫硝的工藝系統(tǒng)主要由脫硫塔、除塵脫硝一體化裝置、噴氨系統(tǒng)、引風機、熱風爐和煙氣管道等組成。兩座焦爐排出的煙氣(約180℃)首先進入旋轉(zhuǎn)噴霧脫硫塔,霧化的Na2CO3飽和溶液與煙氣接觸迅速完成SO2的吸收,脫硫效率在80%以上;脫硫后煙氣進入一體化裝置時先經(jīng)布袋除塵,再由一體化裝置配備的煙氣加熱模塊加熱至200℃后,與噴入的NH3還原劑充分混合;混合后的煙氣進入低溫脫硝催化劑模塊層,在催化劑作用下NOX被NH3還原為無害的N2和H2O,脫硝效率不低于80%;凈化后的潔凈煙氣(>160℃)經(jīng)過引風機送煙囪排放,小部分煙氣通過熱風爐小幅加熱后回用到一體化裝置煙氣加熱模塊中。該工藝采取先脫硫的模式可以有效控制后續(xù)脫硝硫酸氫銨的生成,為低溫高效脫硝創(chuàng)造條件;一體化裝置可以集中進行除塵、加熱和脫硝,減少管道輸送的熱損耗,模塊化可提高脫硝操作和檢修的靈活性;采用低溫脫硝催化劑可使脫硫后的煙氣僅需小幅加熱即可進行高效率地脫硝。此外,160℃以上的排氣溫度不會在煙囪周圍產(chǎn)生煙囪雨,并可以避免煙氣溫度低于酸露點而引起的煙囪腐蝕。
3 燒結(jié)煙氣凈化技術
燒結(jié)工序新建的兩臺燒結(jié)機均為550m2,單臺燒結(jié)機煙氣量達1.8×106Nm3/h,煙(粉)塵濃度約120mg/Nm3,SO2為300-1000mg/Nm3,NOx為100-500mg/Nm3,較之焦爐煙氣量大得多,產(chǎn)生的大氣污染物濃度也高。燒結(jié)煙氣量、溫度和含水量波動較大,還含有二惡英、SO3、HCl、HF和重金屬等污染物。
傳統(tǒng)的濕法石灰-石膏工藝僅能滿足脫SO2的需要,產(chǎn)生的廢水中重金屬等污染成分難以處置,對NOx的處理若選擇增加NH3-SCR脫硝工藝,則加熱煙氣能耗太高。因此,根據(jù)燒結(jié)煙氣的特點,湛江鋼鐵燒結(jié)工序選擇了活性炭吸附脫硫脫硝工藝凈化燒結(jié)煙氣。該工藝的原理主要是利用活性炭比表面積大、具有大量微細孔的特點,首先對粉塵、SO2、NOx、二惡英和重金屬等有害物質(zhì)進行物理吸附;再利用微細孔內(nèi)活性炭表面存在的一定量活性鍵位催化NOx和NH3的反應生成N2和H2O;吸附于活性炭的SO2和重金屬等通過再加熱脫附,二惡英苯環(huán)間的氧基在活性炭表面催化下被破壞裂解為無害物質(zhì),活性炭實現(xiàn)再生。
燒結(jié)煙氣凈化系統(tǒng)主要由燒結(jié)機頭電除塵、引風機、吸附塔、解析塔、噴氨系統(tǒng)、活性炭輸送系統(tǒng)、制酸系統(tǒng)和煙氣管道等組成。燒結(jié)機產(chǎn)生的煙氣首先經(jīng)過電除塵器脫除大部分煙(粉)塵和重金屬物質(zhì),再由增壓風機將煙氣引入若干個相對獨立的吸附塔中。在吸附塔內(nèi),煙氣與稀釋的氨氣混合通過由活性炭顆粒填充的網(wǎng)格層,大部分粉塵、SO2、二惡英和重金屬被活性炭吸附,NOx與NH3反應轉(zhuǎn)化成N2和H2O后的煙氣經(jīng)煙囪達標排入大氣中,活性炭由輸送機送至解析塔。解析塔上部通過隔層加熱將活性炭加熱至約400℃,SO2脫附后富集送至制酸系統(tǒng),二惡英降解;下部冷卻篩分后的再生活性炭可返回吸附塔內(nèi)繼續(xù)循環(huán)使用。系統(tǒng)可通過調(diào)節(jié)吸附塔內(nèi)活性炭填充量和下料速度靈活地應對煙氣的變化,有效地回收利用SO2,保證脫硫脫硝的效率。
4 球團煙氣凈化技術
鏈篦機-回轉(zhuǎn)窯球團工序煙氣排放量可達1.4×106Nm3/h,煙(粉)塵濃度約為100mg/Nm3,SO2為100-1000mg/Nm3,NOx為150-200mg/Nm3。煙氣中SO2和NOx主要產(chǎn)生于回轉(zhuǎn)窯煤燃料的供熱燃燒,NOx的排放濃度約100-150 mg/Nm3(小于國標特排限值),目前階段暫不需要考慮脫硝處理。湛江鋼鐵球團煙氣中SO2的脫除采用了LJS循環(huán)流化床法,該工藝已在寶鋼股份和梅鋼的燒結(jié)機脫硫得到成熟應用。工藝原理主要是絮狀的脫硫劑在激烈湍動中不斷解體重新被氣流提升,物料在循環(huán)流化床內(nèi)氣固兩相激烈地湍動與混合,氣固間的滑落速度高達單顆;渌俣鹊臄(shù)十倍,極大地強化了傳質(zhì)與傳熱,加之床內(nèi)高達50以上的Ca/S比,SO2可與Ca(OH)2 充分接觸反應并生成CaSO3·1/2H2O和H2O,煙氣中微量的SO3、HF、HCl和重金屬等污染物也在流化床內(nèi)被反應或吸收。
LJS循環(huán)流化床脫硫工藝系統(tǒng)主要由電除塵器、脫硫劑添加和霧化裝置、循環(huán)流化床反應器、布袋除塵器和煙氣管道等組成。煙氣首先通過電除塵器脫除大部分煙(粉)塵和重金屬物質(zhì),再通過增壓風機與脫硫劑一起輸送至循環(huán)流化床反應器。流化床底部煙氣入口設有霧化噴水裝置,可將煙氣溫度降至SO2與Ca(OH)2反應的最佳溫度(80℃)。脫硫劑和循環(huán)脫硫灰在塔內(nèi)進行充分反應。無論煙氣量如何變化,煙氣在流化床下部文丘里以上的塔內(nèi)流速均保持在4-6m/s,煙氣停留時間在6s左右,可保證高的脫硫效率(≥90%)。脫硫后煙氣經(jīng)布袋除塵,氣固分離的脫硫灰可返回流化床內(nèi)繼續(xù)參加反應,凈化后的煙氣通過煙囪達標排放。流化床中氣固之間良好的傳熱、傳質(zhì)效果使得絕大部分硫化物得以去除。用于降低煙氣溫度的霧化水附著在巨大比表面積的脫硫劑顆粒上進入流化床,在塔內(nèi)得到充分的蒸發(fā),保證進入后續(xù)除塵器中的灰具有良好的流動狀態(tài)。此外,煙氣中的脫硫劑在濾袋表面沉降形成濾餅,延長了脫硫劑與酸性氣體、有機污染物等的接觸時間,增加了對酸性氣體、重金屬和二惡英等有害物質(zhì)的脫除率。
5 高爐環(huán)保新工藝技術
湛江鋼鐵5050m3高爐荒煤氣排放量為1.25×106Nm3/h,粉塵濃度高達10-15g/Nm3,
對荒煤氣的回收凈化主要采用了重力除塵和干法除塵工藝:爐頂荒煤氣首先通過上升管和下降管輸送至重力除塵器,利用氣流流速和方向的突變,借助重力和慣性力沉降脫除較大粒度的顆粒物,將粉塵濃度降至約10g/Nm3;再經(jīng)多模塊并聯(lián)的外濾式布袋干法除塵器凈化,粉塵濃度可降至5mg/Nm3。干法煤氣凈化與濕法相比:無廢水產(chǎn)生;煤氣壓降小,余壓發(fā)電量可提高30%以上;含水量低、溫度高,作為二次能源具有更高的熱值。熱風爐采用高效陶瓷燃燒器和減小格子磚孔徑、控制合理燃燒溫度和溫度場均勻分布等新技術,減少了NOx的產(chǎn)生量,凈化后的高爐煤氣作為熱風爐燃料在燃燒過程中產(chǎn)生的煙氣粉塵為5mg/Nm3,SO2和NOx分別為120mg/Nm3和50mg/Nm3,可通過煙囪達標排放。
針對初始濃度達3g/Nm3的高爐出鐵場出鐵時產(chǎn)生的煙氣,湛江鋼鐵設置了兩套1.2×106Nm3/h的煙氣除塵系統(tǒng),經(jīng)袋式除塵凈化后的煙氣粉塵濃度(≤20mg/Nm3)可達到排放標準的要求。對于開堵鐵口煙塵、一次除塵未捕集到的煙塵及高爐爐頂上料主皮帶機頭部、爐頂受料斗處工作時產(chǎn)生的粉塵,在爐頂除塵系統(tǒng)的基礎上新增了爐頂罩,設置于車間的屋脊處,利用頂棚下受限氣流自發(fā)向高處運動并積聚的特性將煙氣引流至爐頂除塵系統(tǒng),提高了爐頂除塵系統(tǒng)的煙氣捕集效率。
同時在爐頂采用TGR爐頂煤氣循環(huán)技術,對料罐均壓后泄壓排放到大氣中的煤氣進行回收,有效減少了煤氣和粉塵的排放。
6 結(jié)語
新建的寶鋼湛江鋼鐵有限公司嚴格依據(jù)國家和地方的環(huán)保要求,落實最環(huán)保的“綠色碳鋼板材生產(chǎn)基地”的社會承諾,對大氣污染物排放占比較大的煉鐵廠各個工序生產(chǎn)采取了較為全面的防治措施,針對不同工序各自的特點合理地選擇環(huán)保工藝技術,實現(xiàn)了排放達標。